Market Overview
The U.S. is BC’s largest export market for lumber and value-added products. The U.S. remains the leading consumer of BC forest products, including lumber and mass timber, as well as a full range of value-added products, such as doors, windows, joinery and finishings, and furniture
With the market moving toward multi-family living, there is growing potential to expand the use of wood into multi-family/multi-storey construction, as well as into non-residential applications (commercial, institutional, recreational and educational).
Opportunities for the BC value-added sector also exist in resort homes, log and timber frame structures, prefabricated housing, cabinetry, shakes and shingles, millwork and finishing, and landscaping and outdoor living.
Photo: The Canyons, Portland, Oregon | Credit: Marcus Kauffman, Oregon Department of Forestry
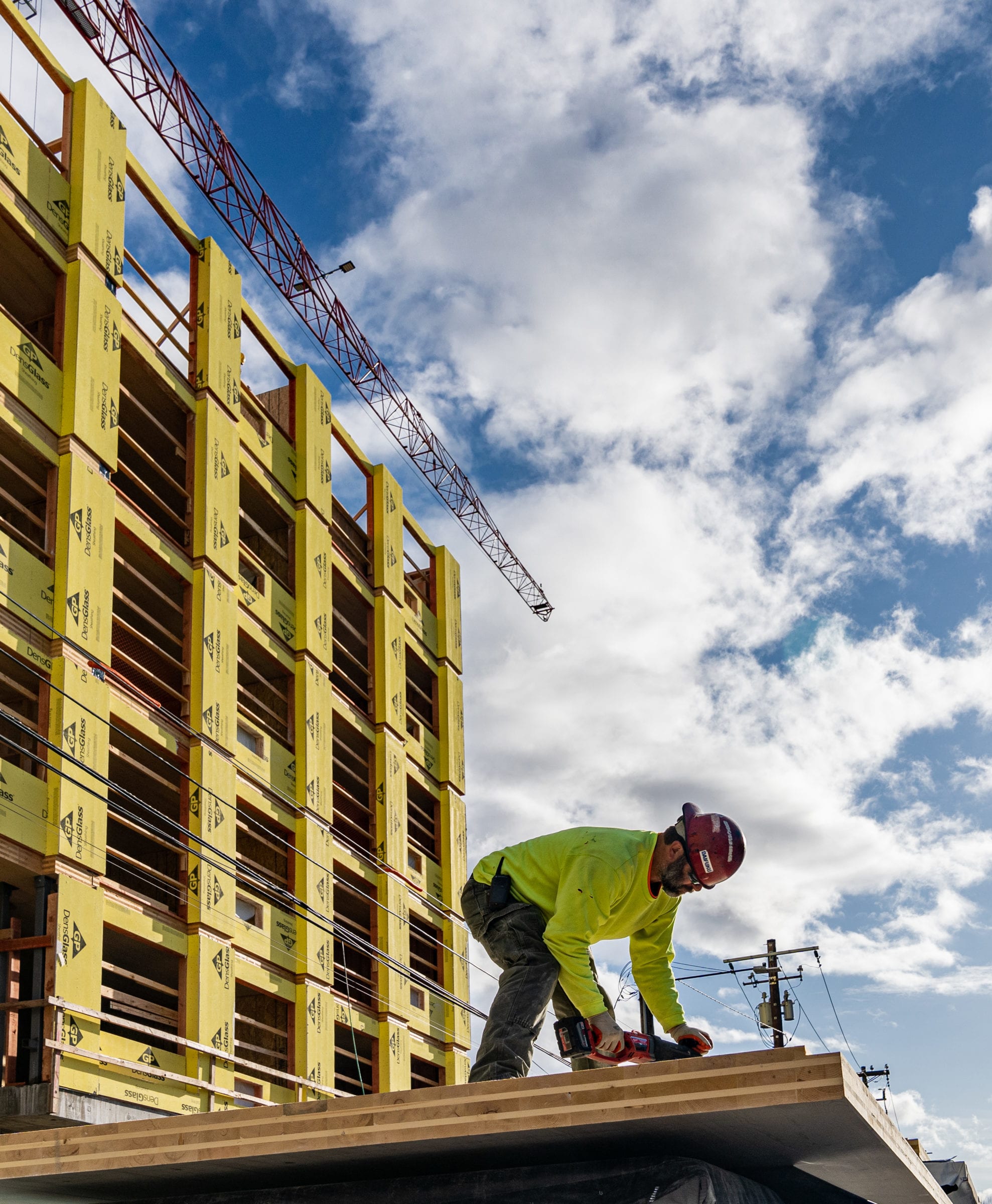