Market Overview
South Korea is a key market for BC wood products, diversifying export risk for the provincial forest sector. The nation’s reliance on imported softwood, combined with government support for green building and the Canada-Korea Free Trade Agreement, creates ongoing opportunities for B.C. wood products. Additionally, value-added wood products present niche market potential.
Photo: Canada Village, South Korea | Credit: Canada Wood Korea
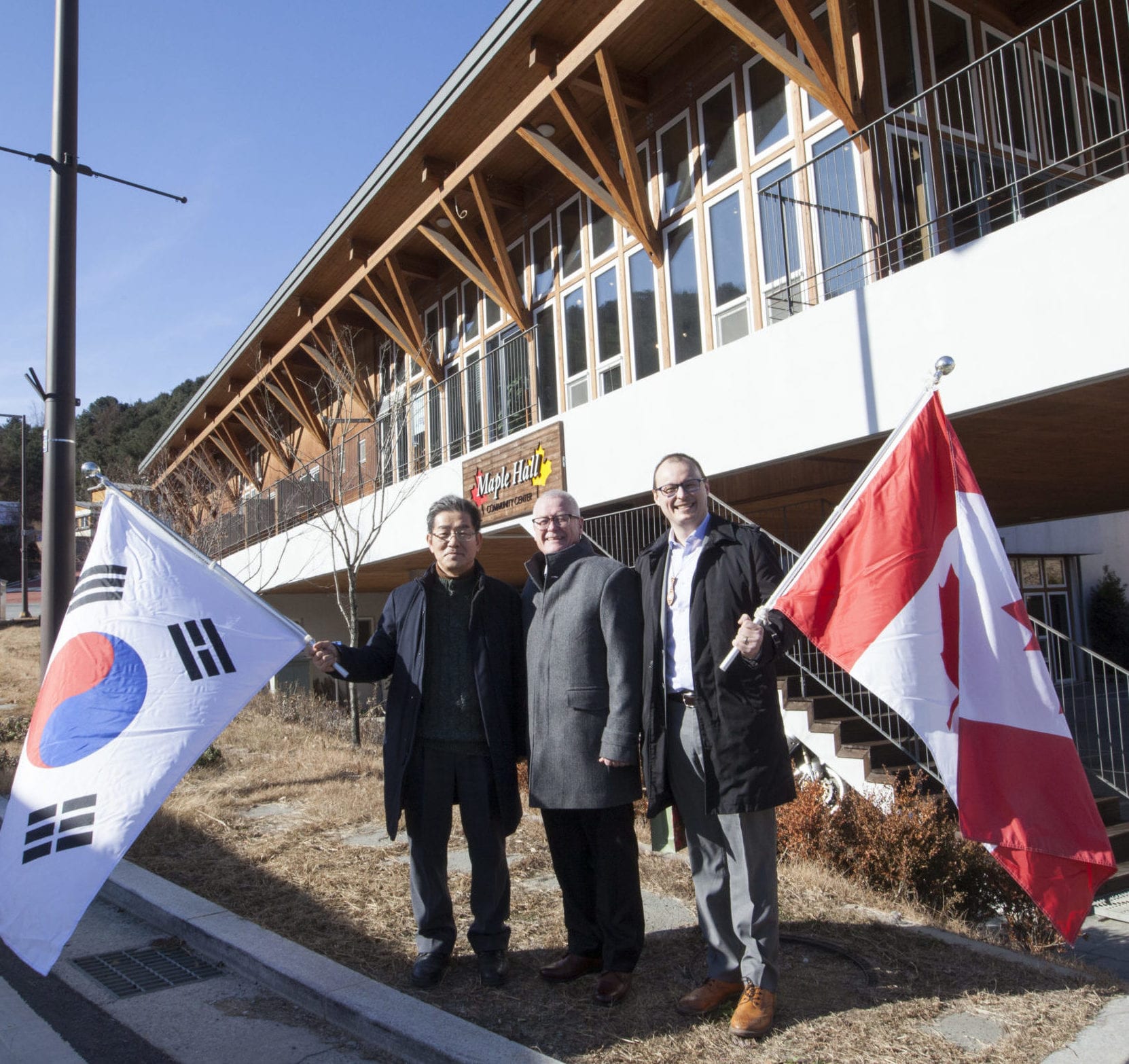